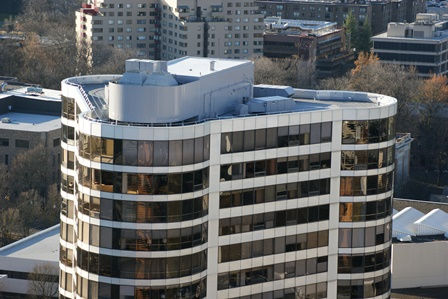
PORTFOLIO PROJECT
Portland Plaza Roof Replacement
ENGAGEMENT TYPE
COMPLETED
COST
OWNER
CLIENT
SERVICES
Existing Building
2009
$850,000
Portland Plaza UOA
Portland Plaza UOA
Roof replacement design, construction administration, quality assurance inspections
OBJECTIVE / BACKGROUND
Portland Plaza is a 25-story residential tower located in downtown Portland that was originally constructed in 1973. The building had been experiencing leaks at the roof level for a number of years and repairs were proving unsuccessful. PRC was initially retained to provide a detailed survey of existing conditions and present a schematic design report with design options and cost estimates for potential replacement systems. As part of the replacement scope, new building maintenance equipment also had to be considered.
STRATEGIES & SERVICES
PRC led the design team that included TM Rippey Consulting Engineers for structural work. To address conditions presented by existing roof geometry and exterior wall maintenance operations, an inverted roof membrane assembly (IRMA) – also called a protected membrane assembly (PMA) – was designed to cover the main roof deck surrounding the penthouse structure, consisting of a waterproofing membrane covered by an insulated overburden system comprised of rigid insulation and pavers, where heavy-duty precast concrete pavers were used at the building perimeter and composite insulated pavers were used in the field of roof abutting the penthouse. A conventional fully adhered single-ply PVC roof system was designed to cover the penthouse structure. The project included significant structural reinforcement of the perimeter parapet wall and implementation of an upgraded mobile davit and adjustable powered work platform for curtainwall and window maintenance. A new perimeter fall protection railing was also incorporated into the project to create a safe work environment for rooftop maintenance. Implementation of the design entailed major roof demolition including removal of a cast-in-place concrete perimeter runway that served the previous building maintenance equipment.
OUTCOMES
PRC’s specialized capabilities drove the success of this project through development of an appropriate project scope, design of critical systems with complex, dynamic relationships and technical requirements, and stringent oversight to ensure a high standard of quality throughout the installation process.
